La UE formuló su plan de protección ambiental en 2007 y se espera que logre este objetivo para 2020. El objetivo es reducir el consumo de energía y las emisiones de gases de efecto invernadero en Europa en aproximadamente un 20% en comparación con 1990, al tiempo que aumenta la participación de nuevas energías en la UE al 20%
Como la economía más grande de Europa, Alemania representa aproximadamente el 20% de las emisiones totales de CO2 en Europa, y es un importante emisor de gases de efecto invernadero. Aunque Alemania ha logrado algunos resultados en la reducción de emisiones, todavía tiene la gran responsabilidad de reducir aún más las emisiones.
Para lograr el objetivo de ahorro de energía, Alemania debe producir de manera más efectiva y continuar reduciendo las emisiones de CO2 de los automóviles. Con el fin de promover la reducción de emisiones nocivas, el Parlamento Europeo ha establecido un límite de 95 g / km de emisiones de CO2 para todas las empresas automotrices para 2020. El límite es de aproximadamente 4 litros de gasolina o 3,5 litros de combustible diesel consumidos por cada 100 kilómetros . Si se excede el límite máximo, el fabricante será multado fuertemente.
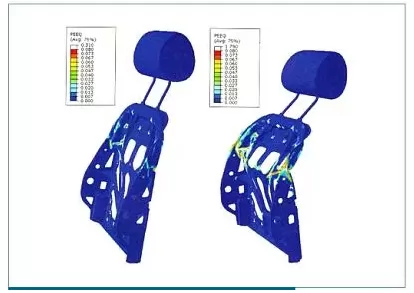
Ahorro de costes:
El diseño de una estructura ligera en el automóvil es muy útil para lograr el propósito de la protección climática de la UE. La base para lograr este objetivo no es solo el uso de materiales livianos, sino también el uso continuo de estructuras livianas. De esta manera, no solo el peso del cuerpo se puede reducir en gran medida, sino que también se puede maximizar la carga de los componentes, y los enlaces tecnológicos se pueden acortar en gran medida. En la actualidad, se puede utilizar una estructura de respaldo de aleación de magnesio fundida a presión ligera y de alta resistencia para reemplazar el respaldo de asiento de acero compuesto por múltiples componentes, lo que permite la posibilidad de reducir el peso.
En el marco de este documento, se proporciona un esquema de optimización, que puede reemplazar la estructura original de acero y lograr el objetivo de reducción de peso y mejora de la resistencia a través de una variedad de esquemas de diseño. El uso del sistema de fundición individualizado para analizar el proceso de fundición puede encontrar las debilidades en el proceso de fundición y optimizar las debilidades. Este método ha señalado la dirección del concepto de diseño para realizar el desarrollo general de piezas moldeables, y se ha convertido en la idea dominante para el desarrollo sostenible de piezas livianas en la industria automotriz.
Los proveedores de automóviles también deben cumplir con los requisitos de protección ambiental, con emisiones de CO2 de 0 g por kilómetro para vehículos eléctricos. Aunque se reducen las emisiones en la industria automotriz en general, según la situación actual, los vehículos eléctricos y los vehículos híbridos solo pueden aumentar a 3 millones para 2020, mientras que los vehículos de combustible tradicionales aumentarán en 30 millones, o incluso más de 100 millones. (Figura 1).
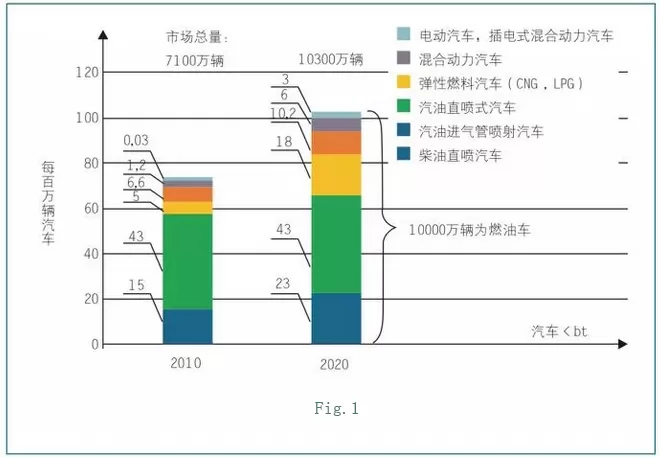
Para lograr el objetivo de la Unión Europea, la adopción de una estructura ligera en los automóviles es la clave para garantizar que se cumplan las condiciones previas. Según la investigación de McKinsy, aunque el aumento en el peso corporal puede compensarse con tecnología de motor de ahorro de energía o dispositivos de accionamiento eléctrico, la proporción de componentes livianos en automóviles también debe incrementarse del 30% en 2013 al 70% en 2030. Accionado por batería los automóviles aumentarán en aproximadamente 250 kilogramos debido al gran peso de las baterías. El chasis y los frenos del vehículo soportarán mayores cargas, por lo que los componentes deben ser más robustos y capaces de soportar cargas más pesadas.
El potencial estructural ligero de los asientos de automóvil es un tema muy interesante. Aunque las estructuras de asiento de magnesio, como Mercedes SLK, se han utilizado en algunos automóviles, las estructuras de chapa de acero todavía representan una gran proporción. Por lo tanto, en este estudio, necesitamos fortalecer el desarrollo del potencial estructural liviano. El propósito es reemplazar el respaldo del asiento de acero hecho de múltiples componentes por una estructura de respaldo de magnesio integrado de alta resistencia y peso ligero. Finalmente, se fabrica un componente ligero de aleación de magnesio con una resistencia comparable al componente original.
Concepto y diseño de fundición a presión de aleación de magnesio
Los puntos clave de desarrollo se introducen en el diseño de la parte posterior (Fig. 2) a continuación. Esta es una estructura de asiento utilizada en automóviles de alta gama producidos en masa. Este tipo de asiento se ha utilizado como la configuración estándar del paquete de material de cuero motorizado V8, y también tiene la función de ajuste eléctrico del reposacabezas.
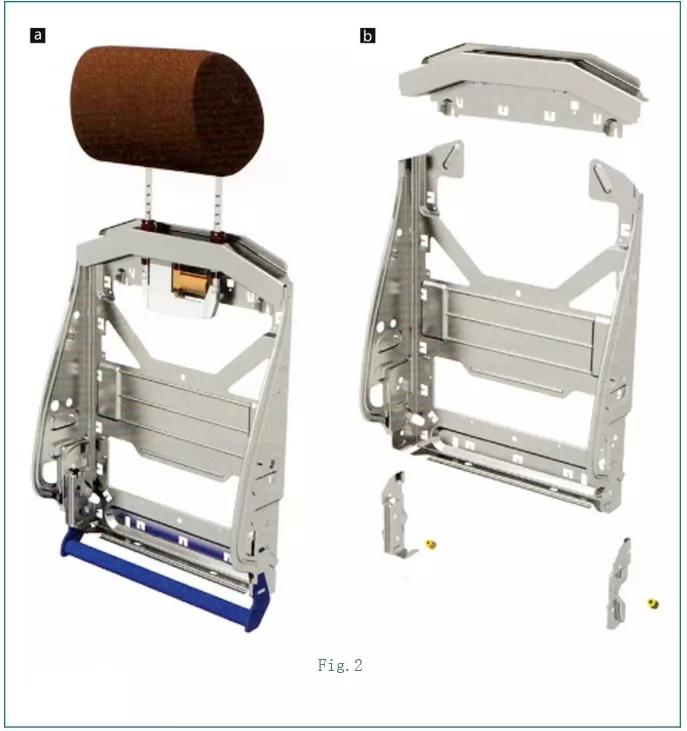
En primer lugar, la estructura real del respaldo se importa al módulo CAD. El modo de conexión del conector con el soporte de la almohada y la estructura trasera del asiento es exactamente el mismo que el prototipo, por lo que puede simularse lo más real posible.
La estructura de placa de acero original consta de seis partes, cuatro de las cuales están estampadas y prensadas. Se requieren un total de dieciséis soldaduras para que todos los componentes se ensamblen y finalmente se rocíen con pintura antioxidante (Fig. 2). El peso total es de 3.24 kg.
El primer objetivo es rediseñar y reconstruir el respaldo del asiento que consta de seis componentes, incluido el proceso de fundición a presión de aleación de magnesio. Esta parte está hecha de aleación AM60 (EN-MC MgAl6Mn), que puede cumplir con los requisitos integrales de capacidad de moldeo, alargamiento y resistencia a la tracción. Las piezas fabricadas pueden cumplir al menos los requisitos de resistencia especificados en la inspección estándar. Las piezas de magnesio no solo pueden absorber la energía de la deformación dañada, sino también realizar la estructura original de la placa. Finalmente, la simulación de fundición de la estructura geométrica se lleva a cabo utilizando el análisis de simulación soft year, y se evalúa la operabilidad. Al comienzo de este artículo, la estructura de losa original se evalúa mediante análisis FEM (modelado FEM-FEM), y se obtiene el valor de referencia. El valor de referencia se utiliza como parámetro de carga del análisis. La fuerza 890N se aplica al reposacabezas en la dirección opuesta a la dirección de conducción. El valor de la fuerza es la fuerza mínima que los componentes pueden soportar bajo las auditorías de la UE / CEPE. Si el respaldo puede soportar la carga, aumente gradualmente el valor de la fuerza hasta que se produzcan grietas o inestabilidad en las piezas.
Del mismo modo, la simulación FEM también es necesaria para las fundiciones de aleación de magnesio. El primer diseño (Figura 3) es una estructura geométrica con ángulo de dibujo adecuado para el proceso de fundición a presión. La posición de conexión de la estructura del asiento y el reposacabezas, y los ganchos del cuero y otras estructuras huecas importantes están dispuestos en la posición original de la estructura de la placa. El componente pesa 1,45 kg, que es más liviano que la mitad del peso del respaldo de acero. Se colocan bordes rígidos insuficientes en la sección de transición del soporte transversal a la pared lateral, que solo puede soportar la fuerza de 325N, por lo que la estructura no ha pasado la inspección.
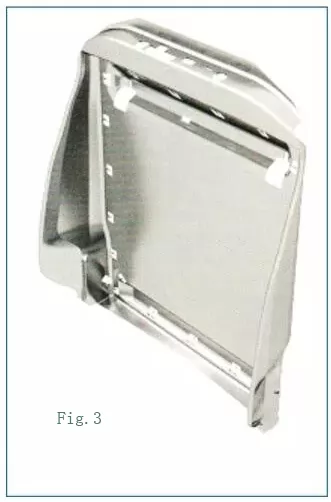
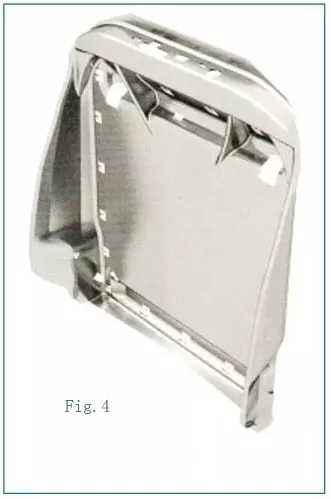
En primer lugar, la estructura del respaldo de segunda generación está optimizada, y la rigidez de la estructura está optimizada. Es decir, se agregan bridas a la riostra transversal superior de toda la pared posterior, lo que fortalece el borde entre la pared lateral y la riostra transversal, y las costillas se colocan en la parte posterior de la riostra transversal (fig.4). Esta medida relativamente simple pero muy efectiva aumenta en gran medida la capacidad de carga a 1406N. Con este cambio, el peso de los componentes aumentó a solo 1.52 kg en comparación con la primera generación. Al comparar la simulación FEM del respaldo de la placa con el respaldo de fundición de magnesio de segunda generación, se puede encontrar que el respaldo producido en masa puede soportar una carga superior a 890 N y solo necesita modificarse adecuadamente (Fig.5).
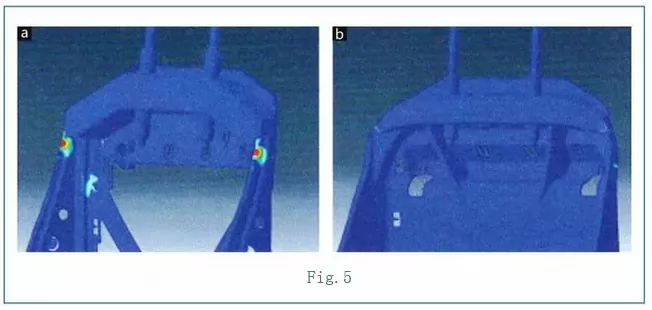
El diseño de optimización de tercera generación se desarrolla sobre la base de la simulación FEM anterior y el diseño efectivo de laminado de bordes que aumenta la rigidez. El diseño de engarzado atraviesa toda la parte, mejorando aún más la altura. Además, con el propósito de reducir el peso, el área hueca se incrementa aún más. Esta versión (Fig. 6) adopta por completo una nueva estructura de diseño. Se adopta una nueva estructura en la sección de transición del refuerzo transversal, que elimina el borde afilado que es propenso a la concentración de tensiones antes. Los resultados del análisis FEM muestran que el componente puede soportar una carga de 1691N (+ 81%) y su rigidez se incrementa considerablemente en comparación con la original. Sin embargo, la debilidad de la nueva ventaja se encontró en el análisis de carga. El daño ocurre en este punto vulnerable debido a que diferentes bordes rizados forman un borde curvo (Fig. 7).
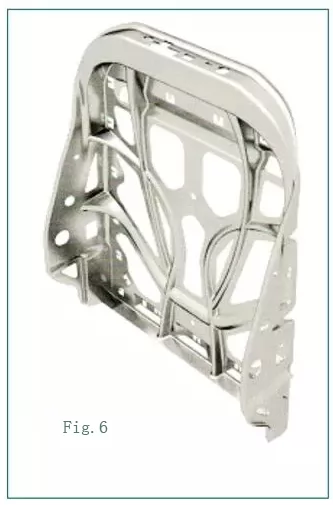
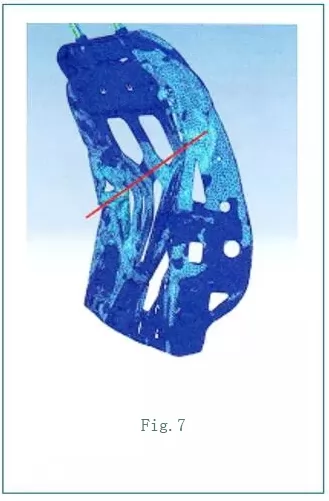
En la etapa de desarrollo de la estructura del respaldo de magnesio de cuarta generación, la rigidez se optimizó mediante un diseño especial de costillas. La estructura básica del componente adopta la misma pared lateral y refuerzo transversal que la tercera generación. El grosor de la pared lateral y el borde superior del refuerzo aumentó de 2 mm a 3 mm. Otro cambio importante es la adición de estructuras de costillas en los lados delantero y trasero de todo el componente (Fig. 8). En comparación con la estructura de placa de acero original, la rigidez aumenta en un 270% y la carga del rodamiento aumenta a 3462N. La estructura tiene la máxima rigidez en la actualidad, y su peso ha aumentado a 2,23 kg. Aunque el peso ha aumentado, sigue siendo mucho más bajo que el respaldo de producción de la estructura de chapa de acero. Basado en la generación anterior de piezas fundidas a presión, la estructura de respaldo de magnesio de 5a generación se desarrolló con el propósito de aligerar. La estructura de la costilla, que no es importante para comprometer la rigidez y la optimización del peso, se elimina en esta estructura (Fig. 9). A pesar de las dificultades técnicas de la fundición, el espesor de la pared se reduce aún más a 1 mm y el área hueca se incrementa aún más. Mediante la modificación anterior, el peso se redujo en un 70% y el peso se redujo a 0,96 kg. La carga sigue siendo mucho más alta que el valor límite de 1299N.
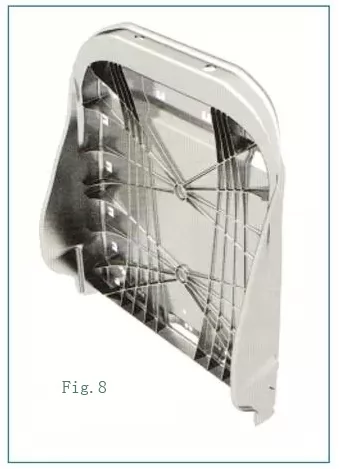
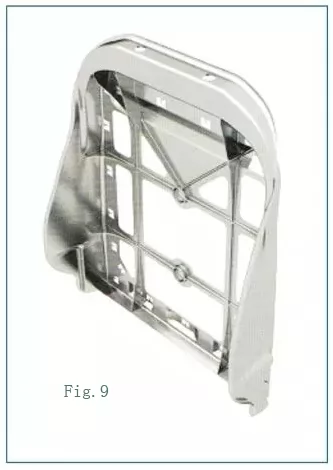
Análisis de simulación de fundición por software
Para verificar que la estructura del respaldo de magnesio de 5ta generación se pueda fabricar mediante tecnología de fundición después de la optimización del peso, el análisis de simulación de fundición se realizó mediante un software de análisis. En primer lugar, debe desarrollarse el sistema de proceso de fundición adecuado para esta estructura. Se debe prestar especial atención a evitar la corriente de Foucault fundida causada por una geometría de fractura inadecuada. La figura 10 muestra un proceso de llenado sellado. El escape se realiza a través de una salida de desbordamiento especialmente diseñada para reducir los agujeros de aire (Fig. 10).
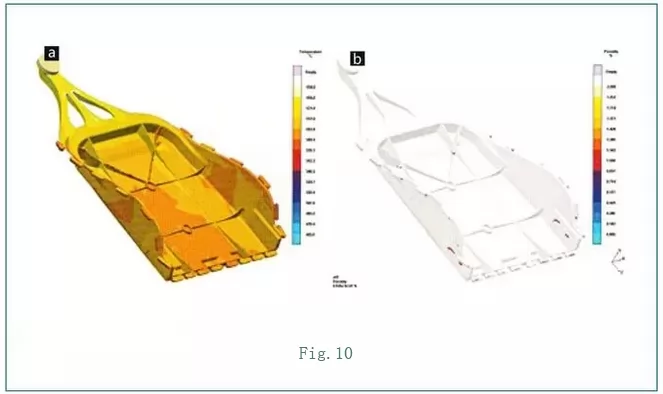
Resumen y discusión
De acuerdo con la investigación sobre el desarrollo continuo de piezas fundidas de magnesio, se descubrió que las piezas fundidas ligeras tienen un gran potencial de aplicación en la industria automotriz. Además del uso de materiales livianos para formar una estructura liviana, pero también tiene un gran valor de aplicación. El objetivo es reemplazar el respaldo de la estructura de chapa de acero compuesta de seis partes por una alta rigidez y piezas de fundición de aleación de magnesio integradas y livianas. La viabilidad del respaldo se demuestra mediante análisis de simulación en varios aspectos. Al mismo tiempo, se muestra que la rigidez de los componentes puede ser mejorada en gran medida por la estructura de la costilla en las condiciones originales. Las diferentes etapas de la evaluación consecutiva pueden verificarse y evaluarse mediante el método de análisis de elementos finitos que se ajusta a las normas de la UE / CEPE (Comisión Económica de las Naciones Unidas para Europa / ONU / CEPE).
Las piezas fundidas de magnesio desarrolladas cumplen los requisitos estándar, incluso en algunos aspectos superan con creces los requisitos estándar, como se muestra en la Figura 11. Otras ventajas de las piezas integradas incluyen pasos reducidos del proceso (prensado, estampado, soldadura, limpieza y pulverización), lo que acorta el proceso . En consecuencia, el consumo de energía se reduce en gran medida, se aumenta el potencial de recuperación y se mejora la utilización de los recursos.
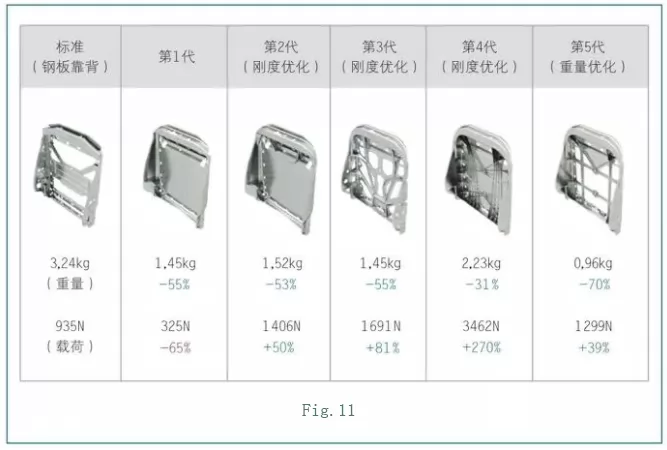
Se puede confirmar que la estructura de respaldo liviana desarrollada a través de este trabajo de investigación no solo puede cumplir con el propósito y los requisitos presentados al comienzo de este documento, sino que también tiene una gran viabilidad de aplicación en la industria automotriz. No solo reduce en gran medida el peso del vehículo, sino que también reduce continuamente las emisiones de CO2. El aspecto económico de este estudio aún no se ha llevado a cabo, y otros procesos y procesos de fundición que ahorran energía se observarán cuidadosamente en el siguiente paso.